From 140km to 170km per month: How AI Increased Tissue Line Output by Over 20%
July 21, 2025A leading tissue manufacturer partnered with FactoryPal to address persistent speed inefficiencies on one of its high-volume lines. Despite significant throughput demands, the line consistently underperformed — producing less output than it was capable of. By deploying AI-driven centerline optimization, the manufacturer achieved a substantial increase in output and stability, moving from 140 km to 170 km of tissue produced per month — all thanks to more controlled and consistent runtime at the right speed.
Unlocking speed without compromise
Prior to deploying FactoryPal, the tissue producer faced a number of operational challenges that hindered optimal performance. Machines often ran below their ideal speed due to suboptimal setups and limited visibility into machine configurations. Production engineers found it difficult to diagnose inefficiencies, while operators lacked the real-time guidance needed to make effective, on-the-fly adjustments.
On the shop floor, static parameters and manual interventions led to inconsistent results and high variability between shifts — especially during night operations. These factors contributed to reduced productivity and left significant performance potential untapped.
Turning data into action
To overcome these challenges, FactoryPal implemented its AI-powered, closed-loop optimization system. Over a 30-day diagnostic period, the system captured performance data across shifts, helping uncover performance losses that had previously gone unnoticed.
By analyzing this data, the AI identified a stable speed that the line could sustain more consistently. Key machine parameters were then optimized to support this target speed. Operators were equipped with real-time, shift-specific recommendations — integrated directly into their workflow — helping them make confident, data-driven decisions on the shop floor.
Importantly, the system continued learning and adapting to evolving production conditions, ensuring that improvements were not just one-off gains, but part of a sustainable shift in performance.
Measurable impact and scalable potential
As a result of this initiative, the tissue producer saw a significant increase in output and productivity, along with greater consistency across all shifts. Performance at higher speeds became the new standard, not the exception.
Beyond the immediate gains, the team also implemented a scalable optimization framework that can now be replicated across additional lines and production sites.
Want the full picture?
Download the full customer case to see the complete performance metrics, before-and-after comparisons, and the exact steps FactoryPal used to help this manufacturer unlock the full potential of its production line.
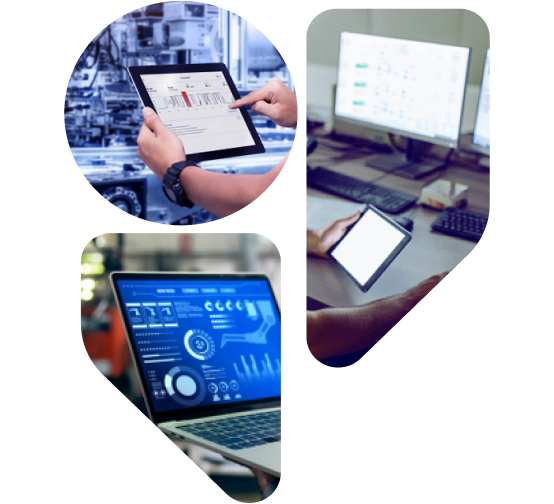
Discover all our other resources and customer cases
From white papers, to guides, to customer cases: Discover all our downloadable resources.
Latest insights from our experts